Fuel From Waste: A Visit to an Ethanol Producer
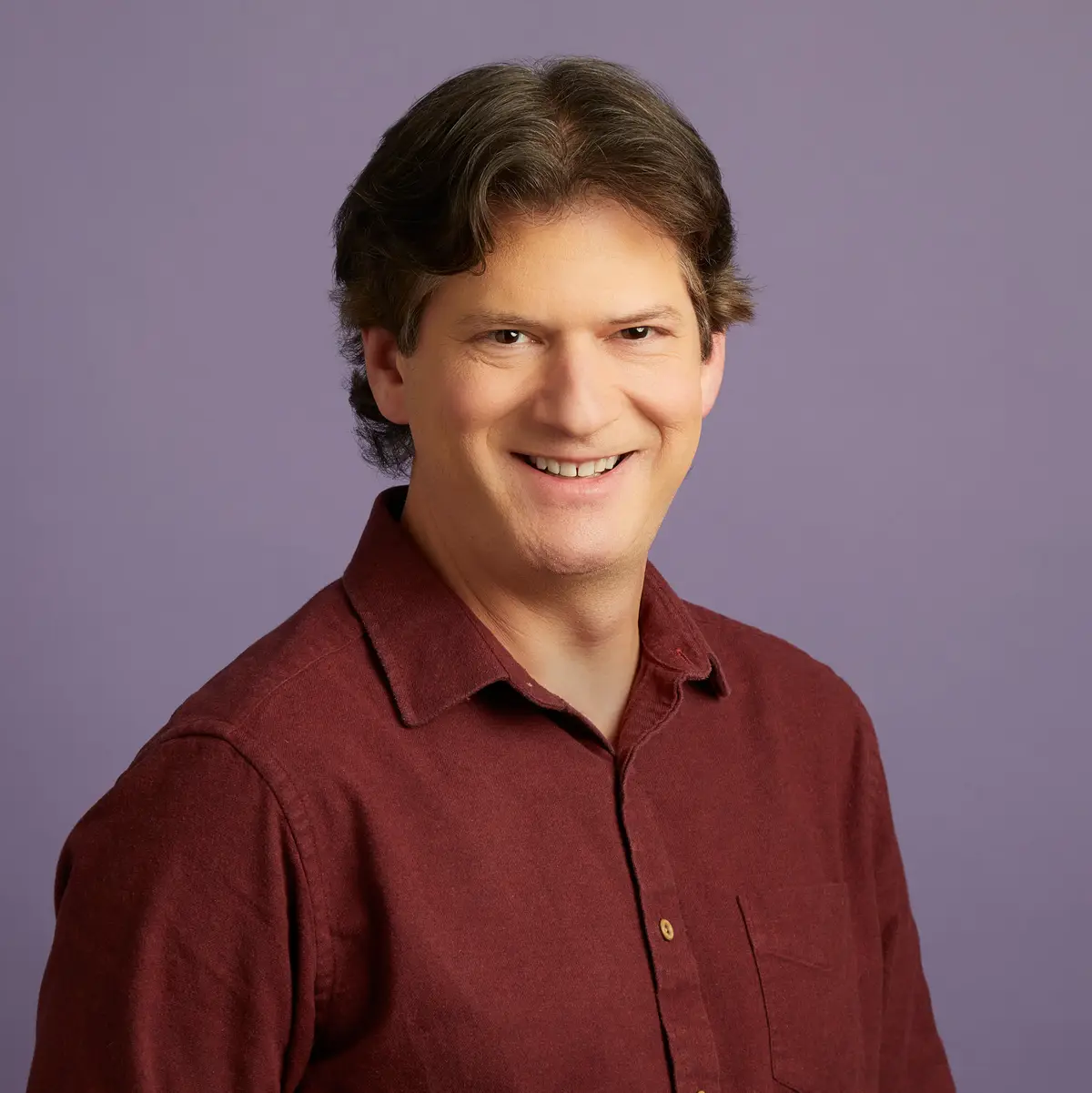
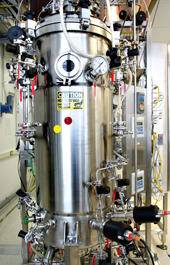
“Could this be it?” I asked myself this question several times the day I visited Coskata’s headquarters in Warrenville, Ill. I drove, puzzled, through an office park, wondering if General Motors’ new partner — a startup that claims to hold the secret to affordable, efficient ethanol production — could really be found in a cluster of lookalike buildings housing an advertising agency, a medical clinic and a company called Yum Brands. I guess I was expecting a towering tank of some sort, complete with a laboratory filled with serious people in the requisite white coats attending to suspended flasks, Bunsen burners and enough tubes and pipes to plumb an apartment building.
The brick structures all appeared to be one story, though, which is too short to house a towering anything. I was about to make another lap around the complex when I saw a parked car with the license plate “ETHNOL 3.” Sure enough, I had arrived at the company, named after a wildlife refuge in Nantucket, that turns garbage into fuel. To GM, which claims the most models capable of running on ethanol/gasoline blends, Coskata is the proverbial chicken to its flex-fuel egg. The automotive giant’s undisclosed investment will support the movement toward an affordable, environmentally sound renewable alternative to imported petroleum — something we currently don’t have.
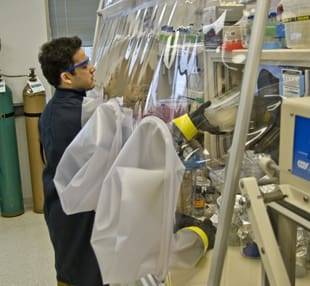
What’s Wrong With Ethanol?
Ethyl alcohol mainly comes from fermented corn. Even in a corn state like Illinois, where E85 is subsidized, ethanol fuel is not priced dramatically lower than gas — especially once you consider the fact that flex-fuel vehicles burn 30% more when running on E85 than on straight gasoline.
Ethanol as a fuel has gotten bad press recently because of its cost, its environmental footprint and the effect on food prices that its growing appetite for corn has. Life-cycle analyses have shown that even though corn absorbs carbon dioxide as it grows, all the energy put into the process — from the sowing of seeds through the burning of fuel in a car — results in nowhere near the desired greenhouse gas reduction. The problem isn’t ethanol, though. As researchers have documented over the past few years, the problem is producing ethanol from a food crop. Studies published recently in the journal Science claim that the carbon dioxide released during corn-based ethanol’s entire life cycle can be twice that of gas if new land is cleared to plant the corn. The studies got a lot of media attention, essentially telling us that producing ethanol from food crops isn’t just the bad idea we thought it was — it’s a much, much worse idea.
Cellulosic Ethanol and Beyond
If ethanol is to come from vegetation, it will have to be from a whole plant — one that requires far less petroleum to plant, fertilize, harvest, transport and process than corn does. Prairie grasses like switchgrass are a likely candidate, but the process to turn the cellulose in plant stalks and stems into ethanol is much more complex than fermenting the sugars or starches that come from food crops like corn. Once we can turn cellulose into ethanol, the corn can be left for the food market and the whole rest of the corn plant can go on to produce what’s called cellulosic ethanol. Coskata has developed such a process, which converts cellulose, plus a whole lot more.
Coskata’s system, which is currently small in scale, works on a variety of source materials, or feedstocks, including shredded tires or other waste material, as well as cellulose such as wood chips. The feedstock goes into a pressurized tank at a temperature high enough to break it down, releasing gases such as hydrogen and carbon monoxide. What emerges from the gasifier is known as synthesis gas, or syngas. Gasification isn’t new; syngas itself can be turned into synthetic petroleum. What’s new is Coskata’s next step, in which microorganisms in a bioreactor feed on the syngas, and those microorganisms then produce ethanol.
Gas-Eating Bugs
Richard Tobey, Coskata’s VP of R&D and Engineering, showed me the lab where these microbes live. As it turns out, the lab coats were blue, but I’ll be damned if one room after another wasn’t plastered with pipes and tubes, petri dishes and vials, more gauges than I’ve seen in a year’s worth of test cars and — oh, yes — an incubator with gloves built into the sides. Tobey ensured visitors that the box is necessary not to protect us from the microbes, but to protect them from oxygen, which would spell their doom.
The microbes have not been genetically modified. They occur naturally and have been isolated and bred for efficiency. Their handiwork is water and 99.7% pure ethanol. The “bugs” are the company’s ace in the hole, but proprietary membranes that separate the water from the alcohol play an important part, too. Because the recovered water reenters the bioreactor, only one gallon of water is needed to produce one gallon of ethanol. Fresh water usage has been a concern for ethanol production, because corn-based ethanol uses two to three gallons of water for each gallon of ethanol produced, and enzyme-based cellulosic processes currently in development can use still more per gallon of output.
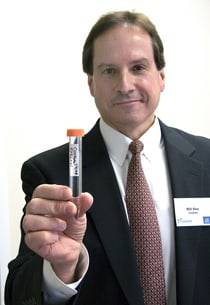
Energy In, More Energy Out
Bill Roe, Coskata’s president and CEO, said the energy equation is equally impressive. A more understandable issue than the carbon released is the amount of energy that goes into fuel production versus how much you get back out. How to calculate this relative to gas is a subject of heated debate, but on a consistent scale, corn-based ethanol has an energy balance of 1.3 (1.3 units of energy out for every 1 unit put into the process), and Tobey says Coskata’s is 7.7.
Where the Coskata process differs most from other cellulosic methods is that it’s not limited to plant matter. The gasifier gladly accepts shredded car tires, municipal waste, plastics that are otherwise unrecyclable — basically anything organic and dry. The tires are favored because they’re carbon-rich, dense and widely available. Tobey said producing five gallons of ethanol would take roughly three tires, 50 pounds of wood or 100 pounds of baled hay or straw. The flexibility, however, is what makes this process so promising. It can be applied virtually anywhere, regardless of the waste stream. Roe said the plants can be built near feedstock sources, perhaps intercepting trash on its way to a landfill, as a way to decrease the economic and environmental cost of transporting it.
Helping offset this cost is the fact that waste producers currently pay to have materials hauled away. Gasification produces little waste of its own, according to Coskata, and some byproducts can be sold. For example, the resulting ash can be used in construction material, such as roofing or paving bricks, or landfilled.
The cost issue is a critical one in alternative fuels, and few investors will gamble on any business that relies on government subsidies. Roe said producing a gallon of Coskata ethanol will conservatively cost $1, unsubsidized. By the time it arrives at a filling station, it should cost the motorist from 50 cents to $1 less than gasoline. As for the environmental cost, Roe said the process releases 84% less carbon dioxide than gas does.
Ethanol’s Future
For years we’ve heard that ethanol’s viability as an automotive fuel will depend on cellulosic sources. “Could this be it?” I asked myself as the plant tour ended. From what I’ve seen so far, it absolutely could be, and then some. We won’t know, though, until we see how well and affordably Coskata’s process scales up. Currently under construction is a 40,000-gallon-per-year demonstration plant that late this year or in early 2009 will begin supplying GM with ethanol. Coskata will also work with ICM, the company responsible for roughly half of the current corn-based-ethanol plants, to build a commercial facility capable of producing 50 to 100 million gallons per year. Its product should be in consumers’ cars early in 2011.
In the interim, Coskata will continue to optimize its microbes and develop strains that produce other fuels, such as butanol, which contains more energy than ethanol — and to experiment with different feedstocks. Asked if he thinks demand for waste would ever grow to the point where fuel producers have to pay to take it, rather than be paid, Tobey said, “It’s a dream of mine.”
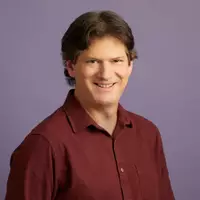
Former Executive Editor Joe Wiesenfelder, a Cars.com launch veteran, led the car evaluation effort. He owns a 1984 Mercedes 300D and a 2002 Mazda Miata SE.
Featured stories
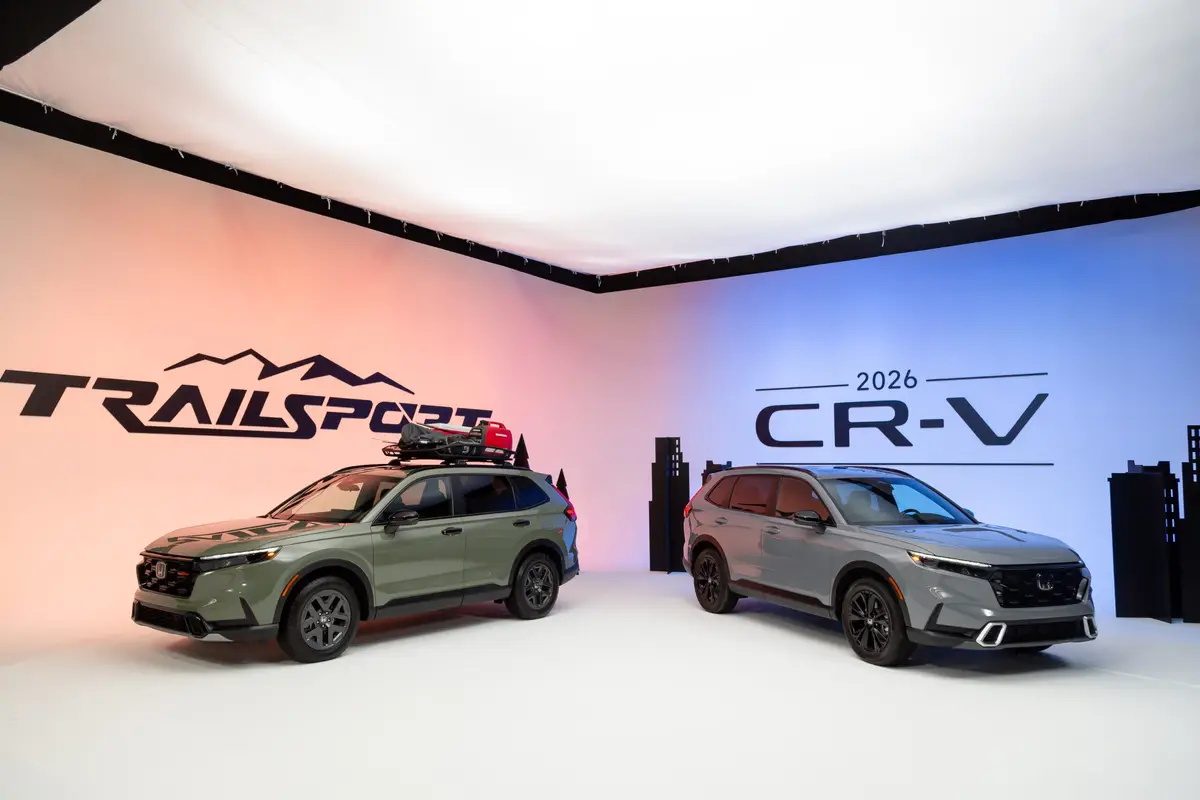
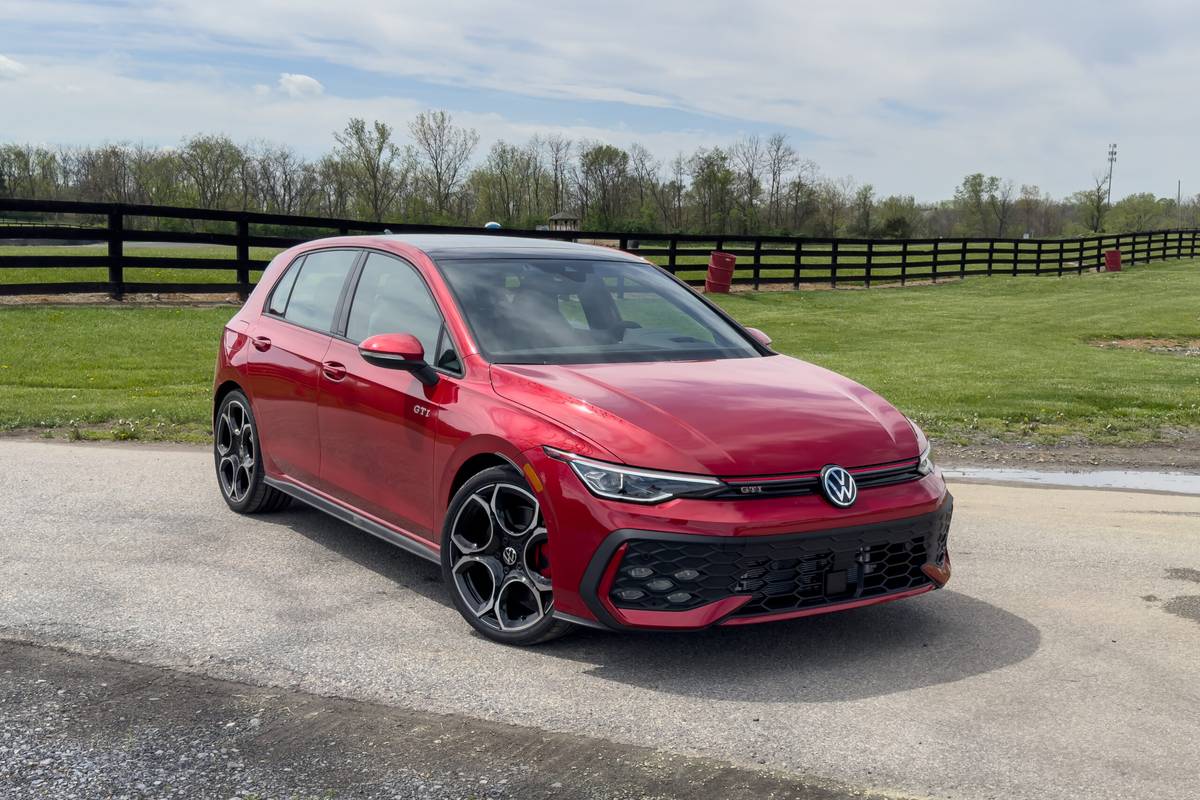
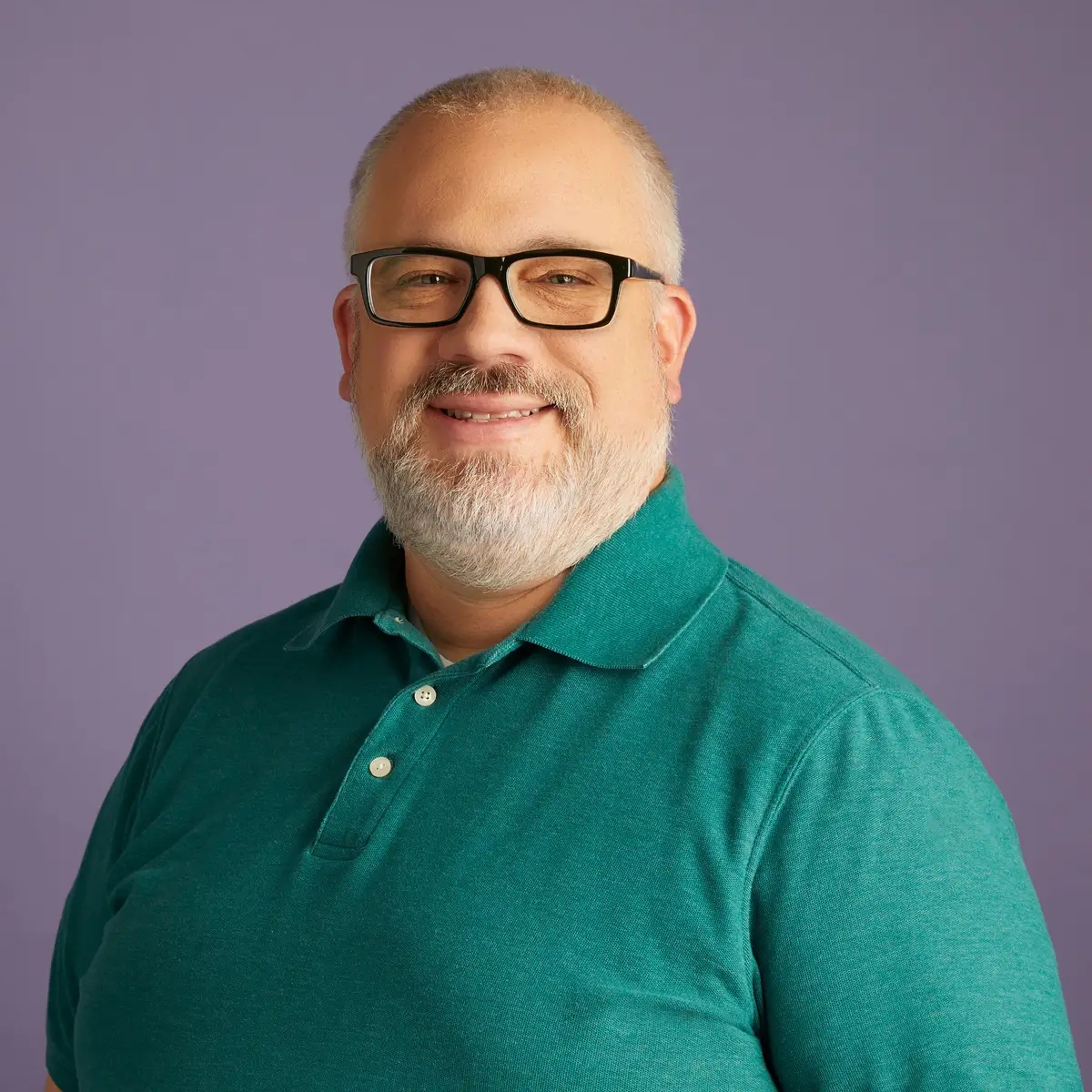
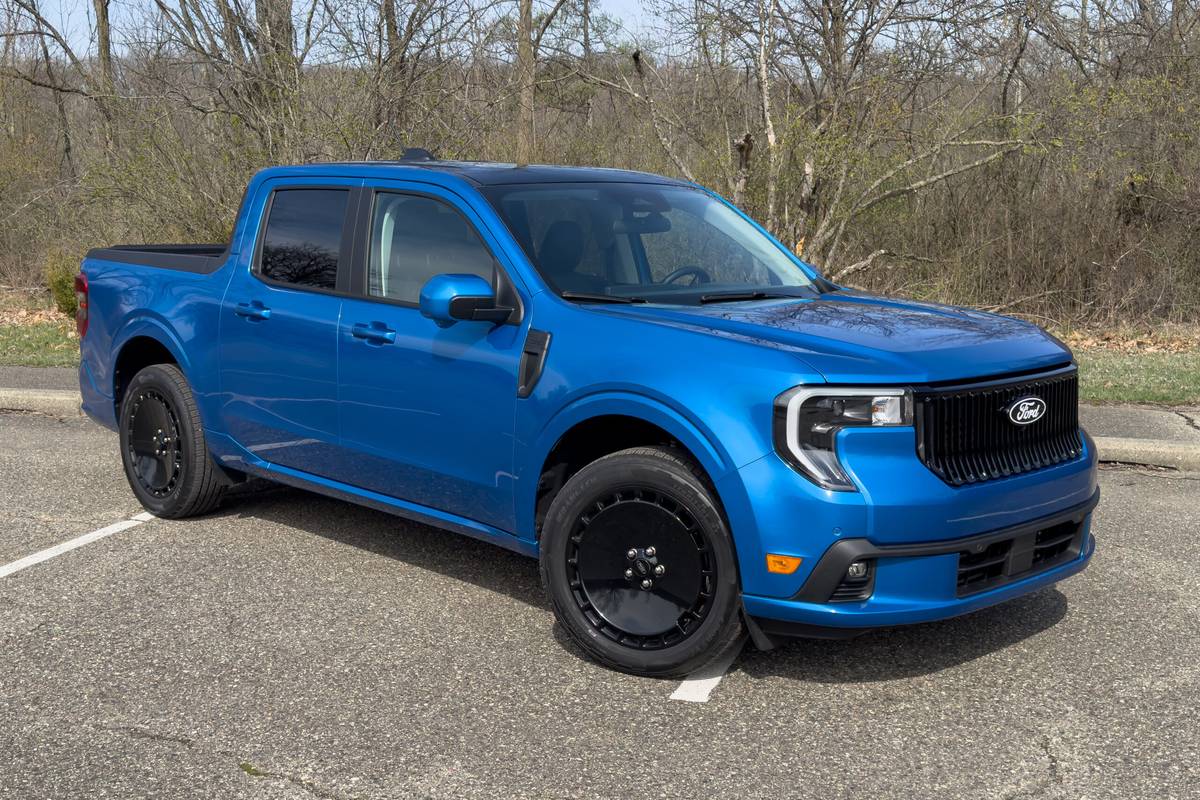