Driven: Protean Ford F-150 All-Electric Pickup Truck
Words and Photos by Ben Wojdyla for PickupTrucks.com
It might not seem obvious, but pickup trucks are the ideal candidates for electric drive systems. Electric motors deliver peak torque at zero rpm to get big loads moving. There’s plenty of room to store massive batteries and heavy-duty components can handle their extra weight.
It’s why Protean Electric – – converted a 2009 Ford F-150 to all-electric drive for the 2008 SEMA show. The unique part: Unlike normal EVs, Protean’s F-150 has in-wheel electric motors, four of 'em, and boy are they powerful. How do we know? Because after three years, we finally got behind the wheel of this alt-powered truck.
Let's back up a moment, though. In-wheel electric motors on trucks aren't a new idea. In fact, one of the first hybrid vehicles was a modified truck built in 1900 by Ferdinand Porsche, and it used so-called pancake motors in the wheels. The reason then is the same as the reason now — mechanical simplicity and packaging advantages. Putting electric motors in the wheels makes sense on a basic level; it puts the power-generating elements where power is needed and frees up space for passengers and cargo.
Looking from the rear forward. Note the hollow beam rear axle shackled to conventional leaf springs and lack of a rear differential. Gear reduction and wheel speed is controlled inside each wheel motor. Battery packs and power cables (orange) are also shown.
Until recently, the biggest reason against using in-wheel motors was that they create too much unsprung weight. Unsprung weight is generally considered the enemy of handling performance. The more weight hanging off the end of the suspension, the harder it is to control the motion of the wheel and by extension, the performance of the vehicle. Generally, more power from an electric motor requires more windings, bigger permanent magnets and added weight.
Protean has taken a different approach that not only increases power, it improves reliability, control and, most importantly, reduces weight.
Protean created an in-wheel electric motor unit that's essentially eight motors in one package. Inside the motor, its rotor looks conventional, with segmented permanent magnets on the outside. The stator, however, is new. Arranged in a circle are eight identical inverter motor controllers, each capable of switching on and off independently and driving the motor at low power individually. Alone, they offer minimum power use, but all together, they switch on and off to provide maximum power and torque.
Closeup look at the right front wheel. Protean's in-wheel electric motor has minimal impact on the independent front suspension, knuckles and tie rods.
This system provides several important benefits, including easy repair and redundancy. But most important is the weight reduction the design allows. Each motor tips the scales around 68 pounds, more than a brake and half-shaft system, but still manageable from a vehicle tuning and dynamics perspective.
Protean has designed its motors as a modular bolt-on system. The motors are designed to use the factory bearing systems, so installation means removing the factory brake system, swapping the bearing onto the integrated mechanical brake/motor unit and bolting it back into place on the axle.
A live axle like the solid rear axle a stock F-150 uses isn't necessary. To prove the point, Protean chucked the factory Ford rear axle in favor of a hollow beam axle, saving considerable weight in the process. They also ditched the rear differential because wheel speed and gear reduction is managed in each of the wheel motors.
Protean’s demonstrator uses a slick inboard braking system much like an old Jaguar E-Type; however, the system can provide regenerative braking. Federal mandates require a mechanical backup system, so traditional hydraulic braking has been integrated into the latest motor design.
How does such a radically different powertrain layout drive in a half-ton truck? A lot like today’s truck. As you might expect from an EV, power comes on strong from the start, and as you reach higher speed, the power output decreases. These aren’t weak motors. Each of the four can generate peak twist of 608 pounds-feet of torque, and continuous output is just as impressive at 368 pounds-feet. Remember, that's for each motor.
Beastly as the motors might be, there’s still a major challenge to overcome: the battery, something Protean makes no bones about. Protean isn’t in the battery business, so the 40-kilowatt-hour battery installed under the bed isn't theirs, just the battery du jour. It's also the truck's weak point right now. Each motor can operate at 84 kwh peak power, about 112 hp, for a grand total of 448 hp. Unfortunately the battery can only output a maximum of 138 kW, or about 185 horsepower. So better battery means bigger power, just like better fuel pump means more fuel, means the potential for more power. Remember, though, that we're talking about a demonstration machine built three years ago. Battery technology has advanced a lot in that time, and so can performance.
The interior has been customized with digital gauges and three push-button controls (next to cupholders) for drive, neutral and reverse modes. The large red button is a kill switch, just in case.
But what about the handling? Making the case that in-wheel motors can be a viable drive system is tough, especially when pitching to a generation of chassis engineers taught that unsprung weight is the worst thing in the world. So Protean did something risky. It didn't tune the suspension at all after the conversion. To compensate for the removal of the drive line, the company placed the hefty battery pack to maintain proper weight distribution and ride height, and that's all it did. The truck still rides on the factory springs and dampers front and rear. It's a tricky way to put the product to the ultimate test. With no suspension tuning working to Protean’s advantage, how does the truck perform compared with the stock setup?
We're not going to gloss over the rougher ride, but considering the circumstances, we're open to believe Protean's view that previous unsprung weight concerns can be overcome. There is a noticeable increase in the amount of vibration translated to the driver compared with a stock truck. Some can be attributed to the 18-inch wheels and lower-profile tires, but in fairness, some comes from the added heft of the motors. It's not disconcerting, though, not even close. It's entirely within reason that with appropriate springs and dampers, you'd never know you were driving something other than a stock F-150, well, aside from the freaky quietness of the vehicle.
Protean's in-wheel electric drive system had no problem moving the F-150 up and over a steep test grade.
In a corner and at speed, it feels similar to a conventional pickup. Such a statement may seem generic, but it belies the possibilities of the system. The highest praise an EV or hybrid can ever get is, “It feels just like a normal vehicle.” That is oddly the goal. Do something revolutionary and make the difference imperceptible. In that measure, Protean has succeeded with this demo vehicle.
What are the odds of this truck, or something like it, making it to production, considering the long odds facing upstart EV companies and their seemingly frequent burnout rate? Protean says it’s watertight financially, claiming it’s nearing its first contract to supply vehicles and has plenty of investor capital available. It expects to make an announcement in the near future of a U.S. production facility for its hardware.
The F-150 demonstrator serves as a “most extreme case” of what Protean can deliver. The company plans to offer hybrid and all-electric vehicle solutions. Protean’s in-wheel system can operate as a through-the-road hybrid, a synchronous axle hybrid, all-electric as is the case with the F-150, or as selectively internal combustion and EV operation. Protean is currently a full generation ahead of the motors installed on this truck, with another generation pending release this summer. The numbers have changed slightly to improve continuous output and overall efficiency, with peak torque down to 578 pounds-feet and 355 pounds-feet continuous with continuous output up to 80 hp rather than 60 hp.
After all this talk of kilowatts and inverter motor controllers and peak versus continuous output, the takeaway is this: Don't fear the future. As much as we all love big, powerful, dinosaur-fueled internal combustion engine-powered pickups, there's room enough for electric trucks, too, or even hybrids. If you think the growl of an IC engine is mandatory for the truck experience, just imagine what having 2,300 pounds-feet of torque on tap might do for your opinions.
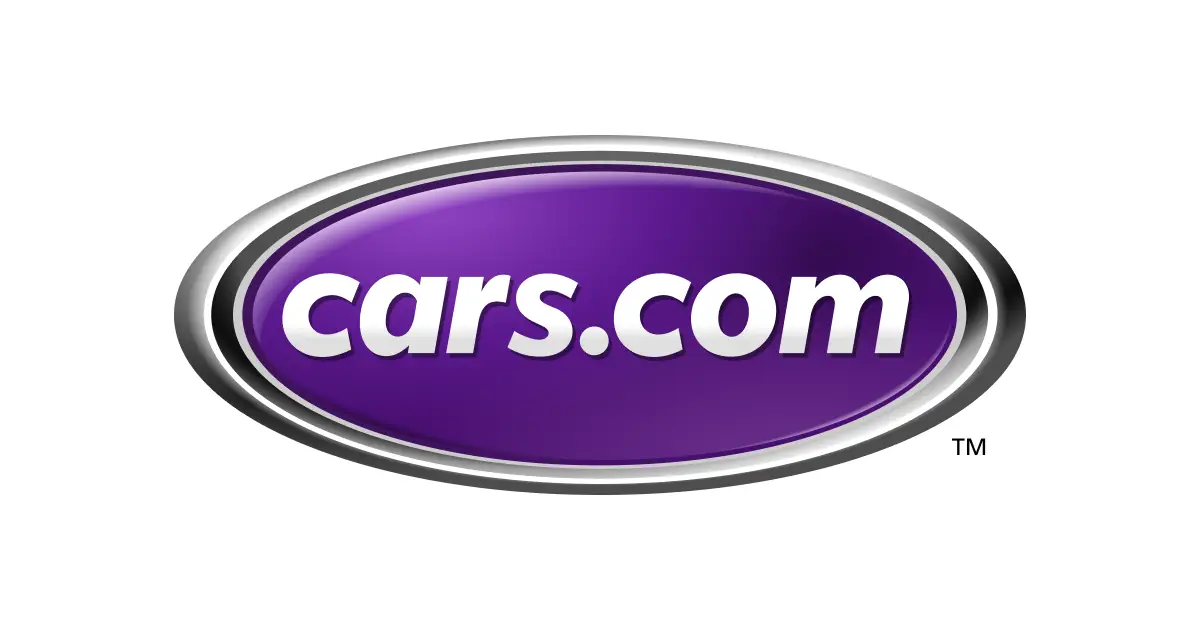
Featured stories
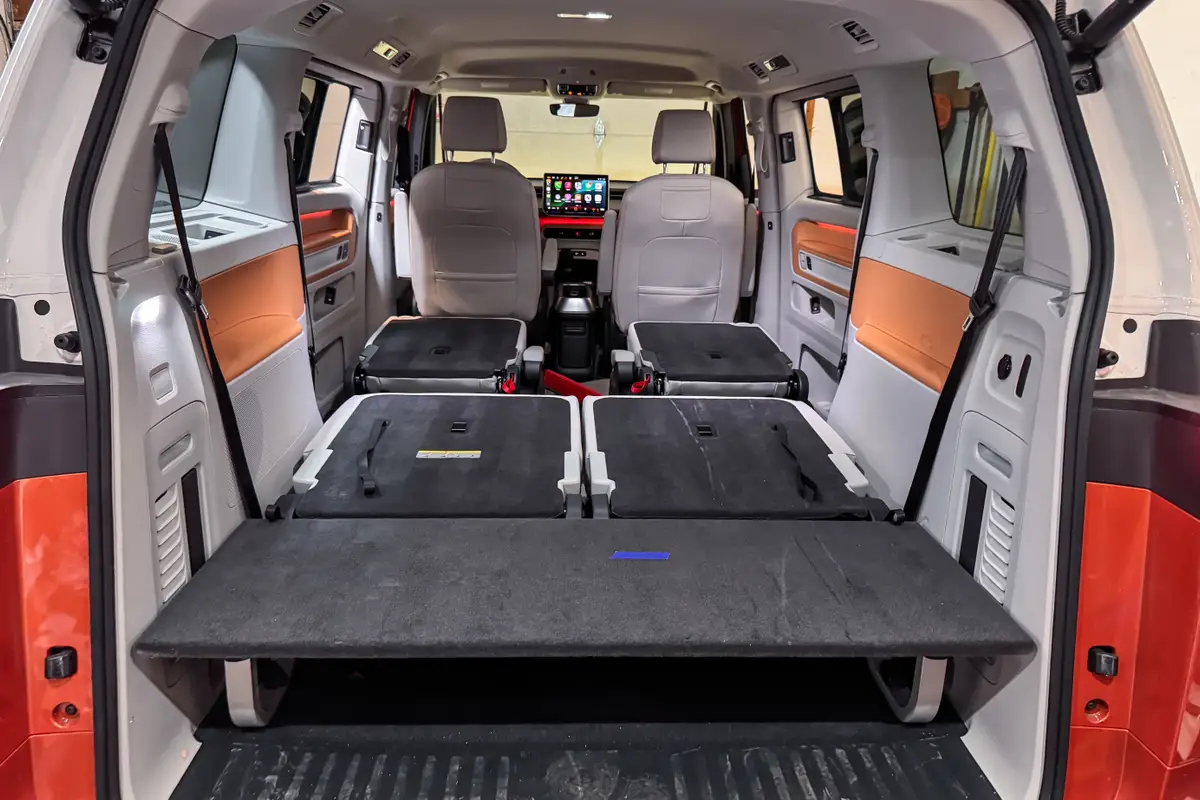
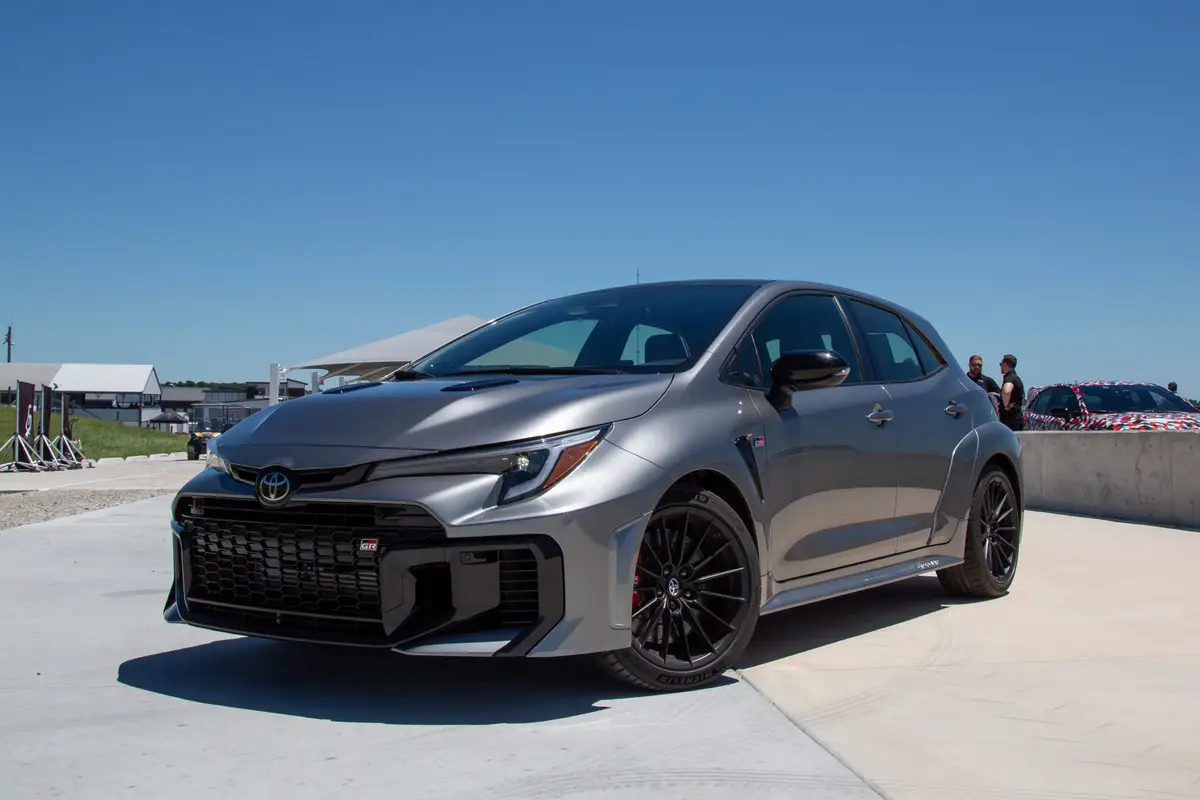
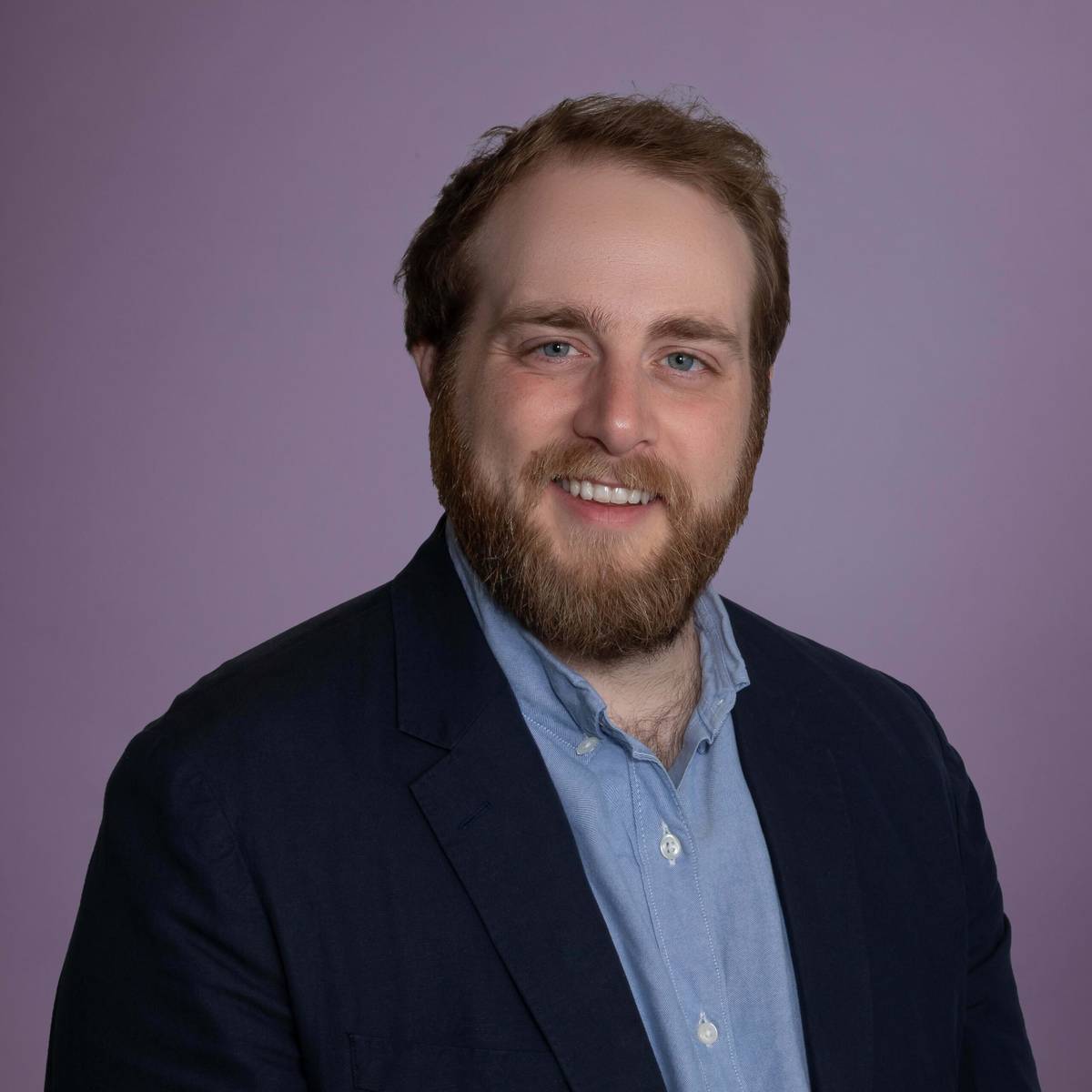
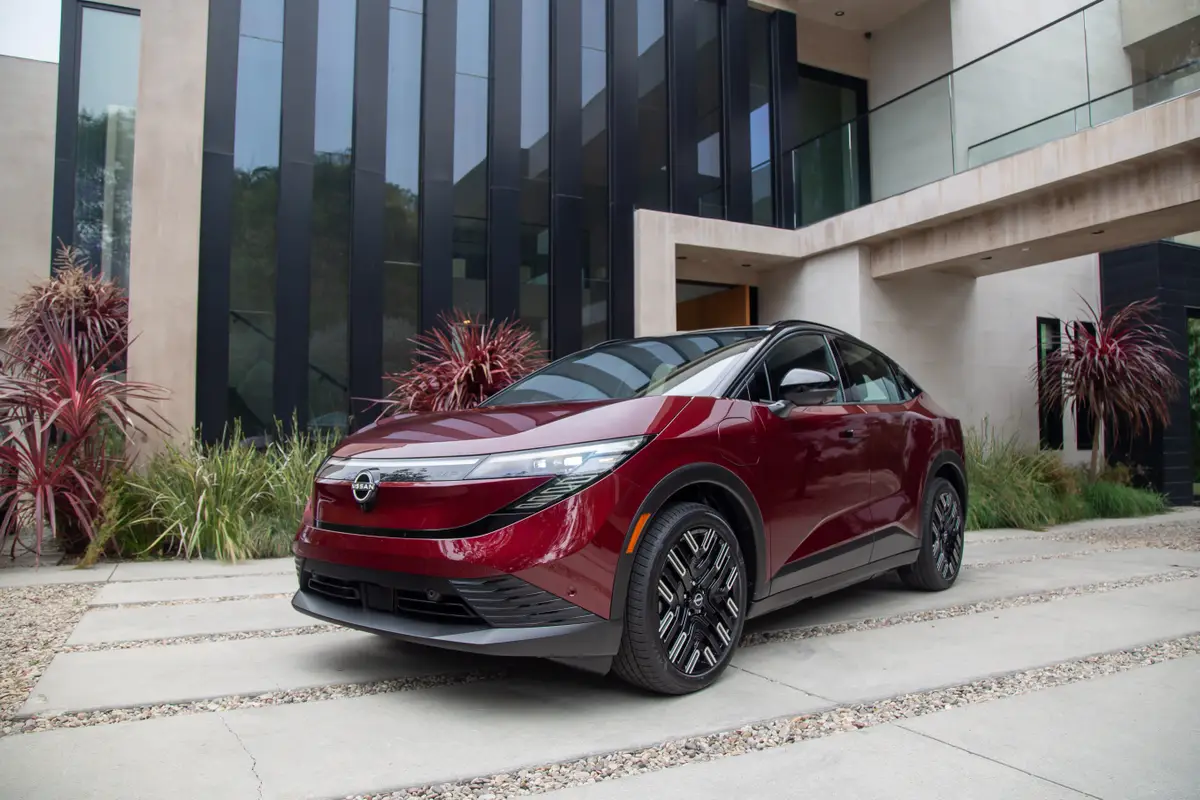