Remembering the '97-'98 Chevy S-10 EV
In the 1990s, GM’s Advanced Technology Vehicles Division developed and built the revolutionary, bullet-shaped EV1 electric two-seater and then gave up on it three years later after low consumer response. Only a few hundred EV1s were leased in five launch markets in Arizona and California.
The EV1 is well-known, but fewer people may know that the same GM division developed a battery-powered Chevrolet S10 compact pickup for fleet buyers. Among its initial customers were the U.S. Air Force and several utility companies, including Virginia Power, Detroit Edison, Boston Edison, Southern California Edison and the Los Angeles Department of Water and Power.
Like its EV1 cousin, the S10 EV was produced in tiny numbers – just 492 over two model years. And like the EV1, after it was canceled along with its parent program, the leased S10 EVs were recalled and destroyed when the leases expired. Why? To protect GM’s proprietary EV technology, protect against liability lawsuits (with 312 volts on board) and protect GM dealers from having to stock out-of-production EV parts. GM probably didn’t want to train technicians to service the vehicles for many years to come.
But whereas the EV1 was a lease-only program, some 60 S10 EVs were sold, and some are probably still in service.
“When some of the utilities were done with them, they put them up for sale,” says Garrett Beauregard, who worked on the EV1 and the S10 EV as an engineer before leaving GM for Phoenix-based Ecotality, where he is now senior vice president of engineering. “We had four of them owned by employees. When I came down here to interview, I was picked up in an S10 electric and driven to the office in it by the guy who would become my boss. He had personalized it with a body kit, side skirts, an air dam and aluminum wheels, and (he) lowered the suspension, so it was kind of sporty-looking. He really loved that truck! Another guy, Tom Convey, had the last one here. He sold it to a physician in Minneapolis.”
Convey remembers that truck very fondly. “The smooth, quick acceleration was like taking off in a light aircraft. The sound of the gear whine reminded me of a turbine engine. If GM made a vehicle like that again, I’d buy it in a minute! I miss that truck!” Beauregard recalls conducting EPA-type dynamometer energy tests and proving-grounds range tests with S10 EVs at GM, and “walking through a room set up for development of the owner’s manual, looking at all the pages and providing feedback on it.”
The S10 EV was essentially a base Chevy S10 short-bed compact pickup powered by a “detuned” EV1 electric drive system (114 horsepower, or 85 kilowatts) to help extend its range. That made the S10 EV front-wheel drive and very heavy at 4,199 pounds, yet it preserved a 951-pound payload under the 5,150-pound gross vehicle weight rating. Of that, 1,400 pounds was the 16.2-kWh lead-acid battery pack tucked between the frame rails under the bed.
To supplement its energy-efficient heat-pump air-conditioning system below 40 degrees, the S10 EV carried a diesel-fuel-fired heater to warm the battery and (secondarily) the cabin. Other differences from the EV1 included a less sophisticated regenerative braking system and its truck-capable wheels and tires. Distinguishing the electric S10s from conventional counterparts were a front air dam and a half-tonneau over the rear of the bed, both to reduce aerodynamic drag.
Another GM engineer with clear memories of the S10 EV program is Gary Insana, who was program manager in charge of the build process. “It was pretty straightforward,” he says. “We had to take out the gasoline engine, fuel system and everything else on the gasoline side, modify the chassis and put in the electric components — the motor, power electronics, heat pump, electric power steering and the large battery pack. We set up a satellite facility just outside the Shreveport, La., S10 plant and did chassis assembly there, then transported the chassis back to the main plant for final assembly.”
Clive Roberts, the GM ATV development engineer who did such a marvelous job of making the EV1 ride and handle as well as it did, remembers working briefly on the S10 EV. “I did a minimal amount of tuning,” he says, “and found the handling pretty gruesome. But I was told by more experienced truckees that was how life was with a heavily laden truck. We played with the rear-axle kinematics to get something bearable and did a small amount of damper tuning, but then I was told to stop by the chief engineer because it was ‘good enough.’ ”
Not surprisingly, cost and range posed major challenges for GM’s S10 electric. List price (for those that were sold) was $33,305, a hefty ticket for a low-range compact pickup. The U.S. Department of Energy financed third-party testing by a company called EVAmerica — now the Idaho National Laboratory’s Advanced Vehicle Testing Activity (AVTA) – and it came up with ranges of 38.8 miles at a constant 60 mph, 60.4 miles at a constant 45 mph and 43.8 miles on the EPA test cycle. Southern California Edison’s three test trucks logged 35 to 43 miles of real-world range on a local urban loop. Newly developed 39-kWh nickel-metal hydride battery packs, an option for the 1998 model year, doubled the truck’s usable range, but at significantly higher cost.
Roberts recalls seeing an S10 EV in China when he was there as GM China’s chassis development director. “We sent five EV1s and five S10 electrics to China for a demonstration program in the Guangdong province,” Insana says. “There is an island there that they were trying to make ‘green’ with a lot of windmills and electric vehicles. I went out there with a couple of technicians to train them, and we swapped the batteries out for NiMH packs. We never did get an order, so that program never went anywhere.”
One S10 EV set records in three world-famous Pike’s Peak Hill Climb competitions. Its efforts are (surprisingly) listed at No. 8 among Chevy’s “Top 10 Moments in Chevrolet Motorsports.” Larry Ragland drove the S10 EV to victory at the 1997 contest.
Why did GM invest money and resources to develop a compact pickup EV in addition to its hugely expensive (and ultimately unsuccessful) EV1 program? “It was a demonstration process,” Insana says. “There were many fleet-type customers with duty cycles that represented good applications for electric vehicles — short drives that could be all electric, then back to the same location for charging each night. The goals were to test the capability of that type of vehicle, to understand that customer base and see how this vehicle would fit that profile, and to test what relevance it would have to those customers’ needs.
“And there were many efforts to get more advanced batteries in those vehicles after we stopped supporting them. Several companies were pursuing outside avenues for advanced batteries because they very much liked the concept of electric trucks, but needed more range.” And that pretty much sums up battery-powered EVs’ toughest challenge today as well.
The charging unit in the photo is an inductive "loop" system, the same type originally used on the early EV1 vehicles, but no longer in use today.
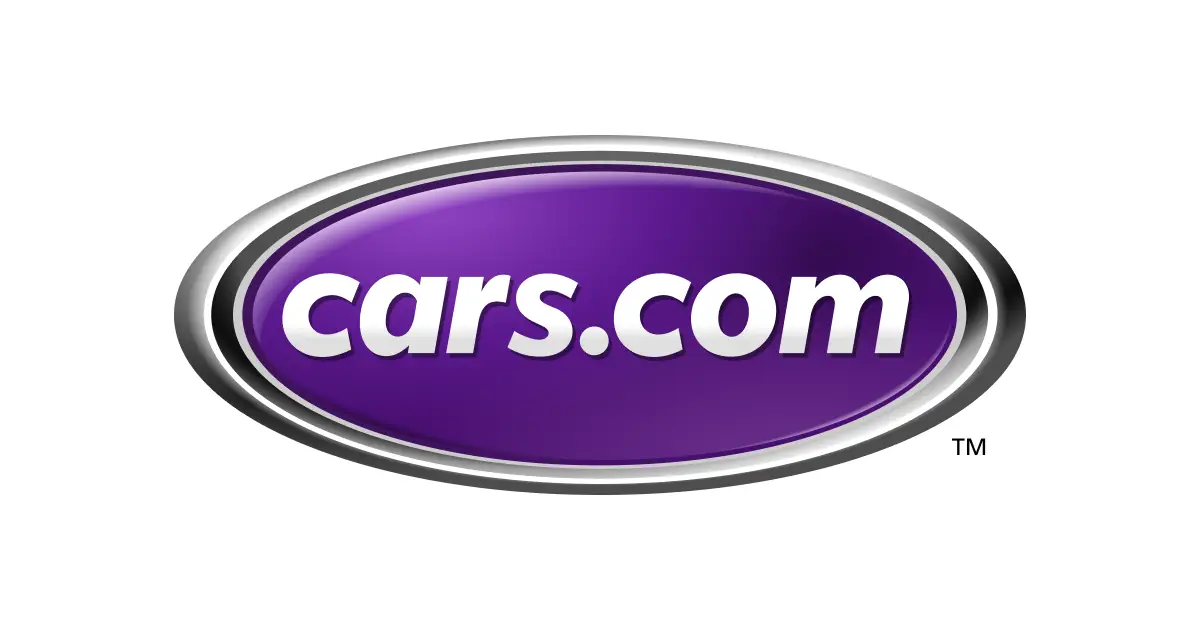
Featured stories
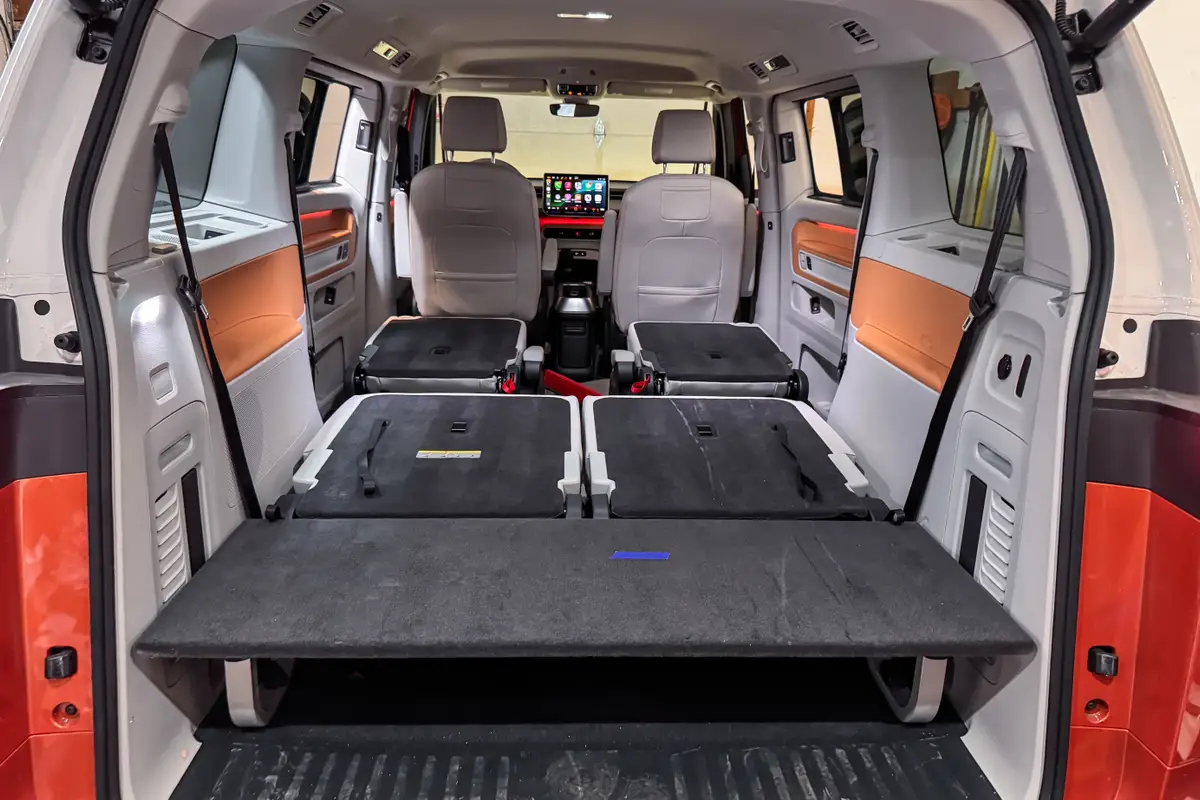
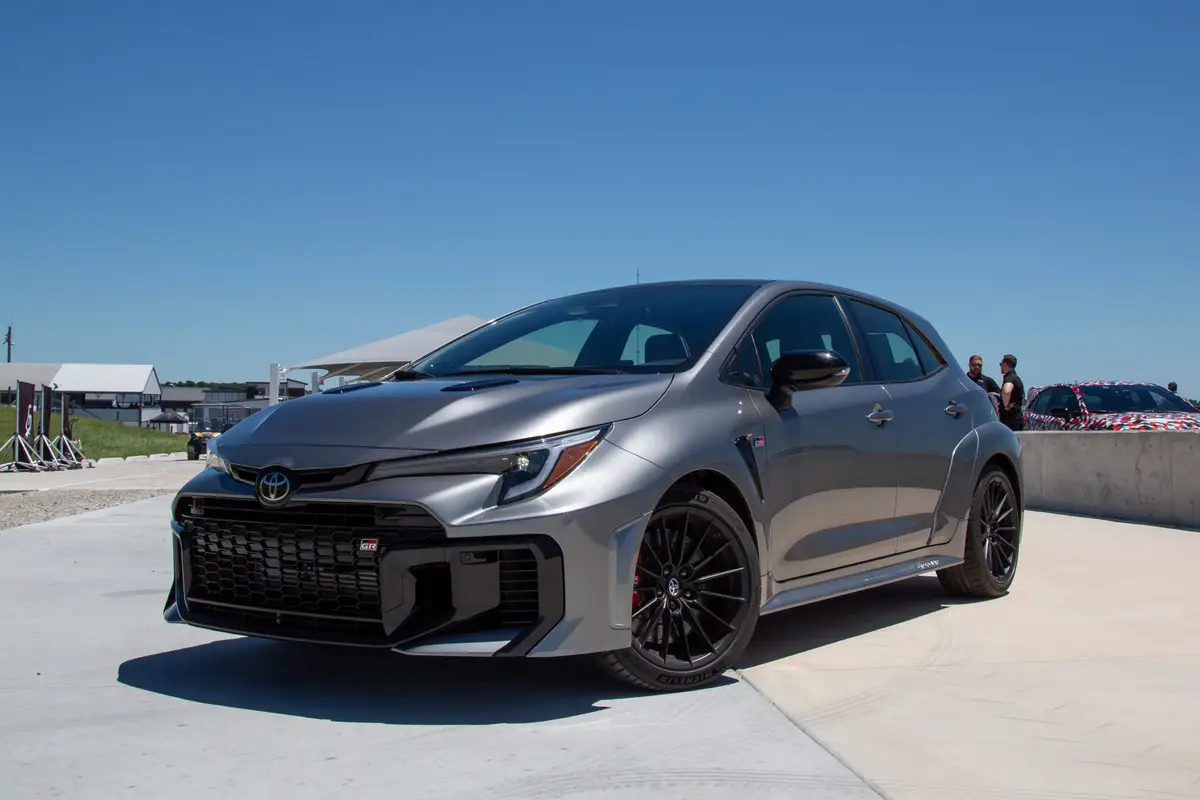
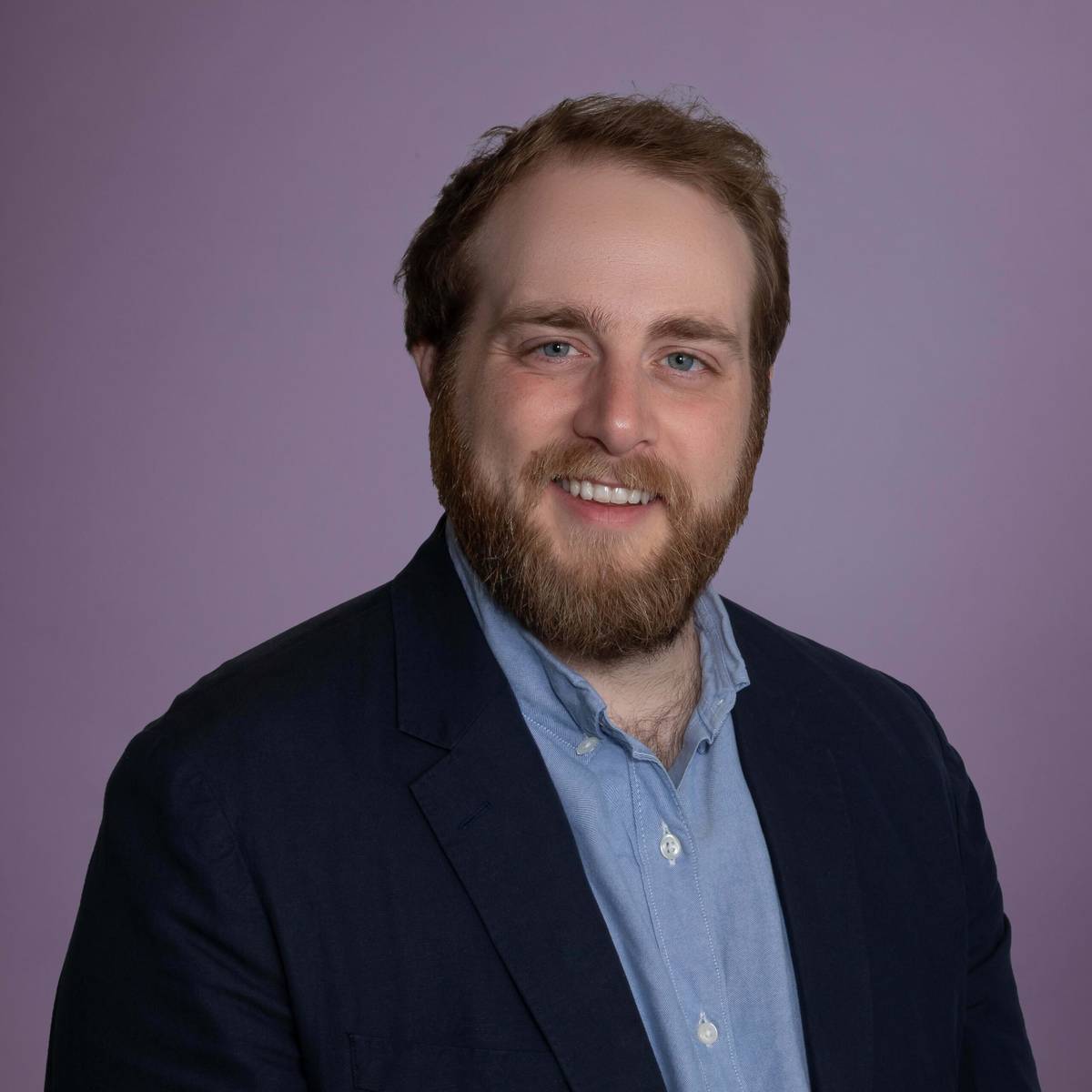
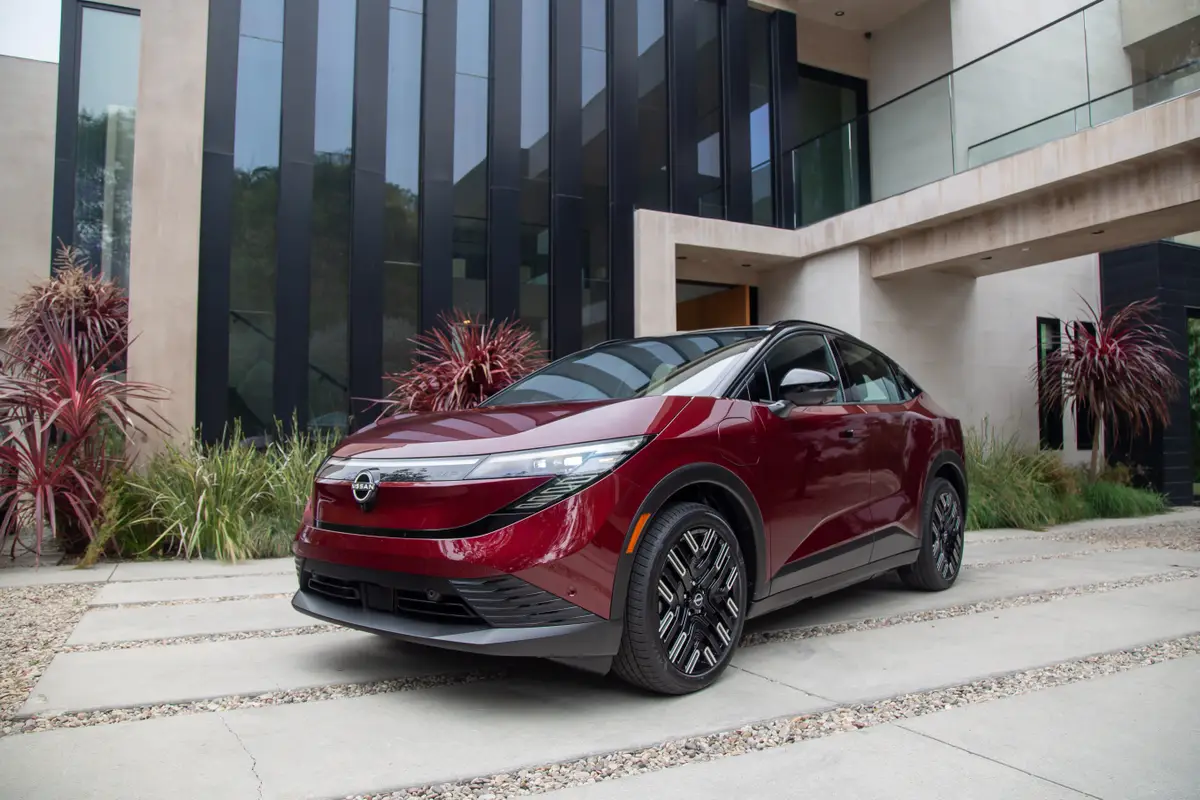